What Is The Body Of A NASCAR Made Of?
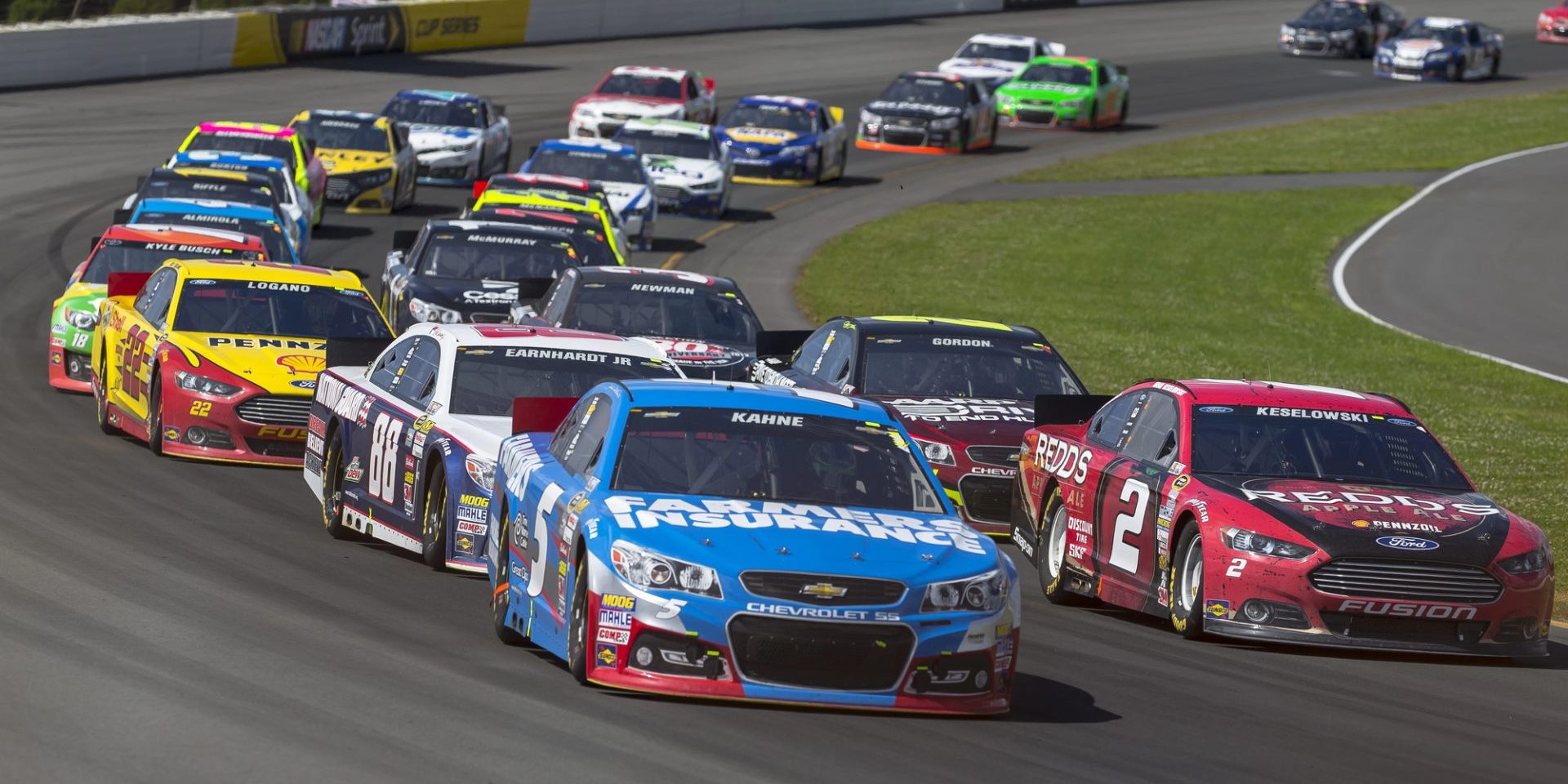
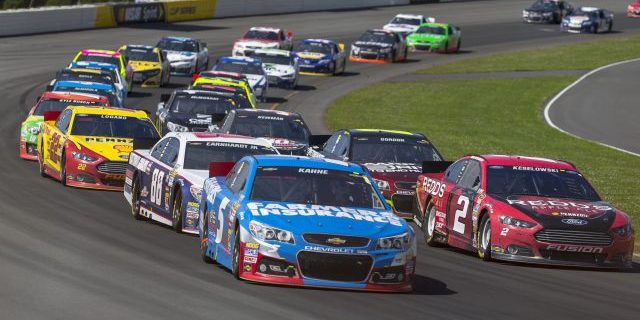
The construction of a NASCAR race car’s body is a complex blend of form, function, and aerodynamics, built primarily for speed and safety. At the core of this construction are the body panels, which are traditionally fabricated from sheet metal. More recently, the industry has seen a shift toward composite materials, notably a mix of fiberglass and carbon fiber. These materials are chosen for their strength-to-weight ratio, an essential factor in high-performance racing. The symmetrical body design of the latest Next Gen race cars is a significant departure from past designs, aimed at enhancing competitive parity by removing the skew that previously allowed for side force advantages.
Safety is a critical component integrated into the fabrication of NASCAR bodies. The evolution of car design continually addresses the safety of the driver, with a particular focus on energy absorption and distribution of forces during crashes. Aspects such as the roll cage, foam inserts, and energy-absorbing walls on the track work together to create a safer racing environment.
The construction process for these bodies involves skilled craftsmanship to ensure each panel meets strict specifications. Panels such as the roof, hood, and deck lid are regulated components that are often supplied by the car manufacturers, ensuring uniformity across the competitive field. The remaining body panels are carefully crafted, utilizing techniques such as hand-rolling on an English wheel to achieve the precise contours required for aerodynamic efficiency and adherence to NASCAR’s stringent regulations.
Table of Contents
Materials and Construction
The bodies of NASCAR vehicles are a complex blend of materials designed for high performance and safety. These materials involve both traditional sheet metal and advanced composites including carbon fiber and fiberglass, each fulfilling a specific purpose in the construction of the car body.
Sheet Metal and Composites
Sheet metal was the go-to material for constructing NASCAR car bodies for many years. It is typically made from steel or aluminum and is known for its durability and ease of repair. Recently, the industry has shifted towards composite materials. These composites are designed to be lighter than sheet metal, promoting better aerodynamics and fuel efficiency.
Carbon Fiber and Fiberglass
Carbon fiber and fiberglass are the primary components of the composite materials used in NASCAR today. Carbon fiber is a strong, lightweight material that contributes to the structural integrity of the race car. Fiberglass, while not as strong as carbon fiber, still offers a good balance between weight and durability, and can be found in various parts of the NASCAR vehicle body.
Composite Material Evolution
The evolution of composite materials in NASCAR has greatly affected the construction of race car bodies. The transition to composite bodies allows for faster manufacturing and assembly, and provides a significant reduction in weight compared to traditional sheet metal. This evolution reflects a continual improvement in the sport’s technology and the drive for performance excellence on the racetrack.
NASCAR Vehicle Structure
The body of a NASCAR vehicle is a carefully designed structure that balances aerodynamics, safety, and regulations. It incorporates a precision-engineered chassis and frame, an aerodynamic body shape fine-tuned for racing, and safety features designed to protect the driver.
Chassis and Frame Design
The chassis serves as the skeleton of a NASCAR race car, essential for both strength and flexibility. It is primarily constructed from steel tubing and follows specific NASCAR regulations. The frame is made up of both round and square tubing, with thickness variations tailored for rigidity and safety. The designs are regimented to a degree, with autosport governing bodies providing templates that dictate the acceptable contours of the car.
Aerodynamics and Body Shape
Aerodynamics play a significant role in NASCAR vehicle performance. Each car’s body shape is sculpted to reduce drag and enhance downforce, enabling higher speeds and better traction. The body is labor-intensive to construct, with NASCAR rules tightly controlling the shape. This is reflected in a standard set of templates, each designed to match different sections of the car to ensure compliance and fairness.
Safety Features and Roll Cage
NASCAR vehicles incorporate advanced safety features focused on protecting the driver. A key component is the roll cage, a robust network of pipes that form a protective barrier around the driver. This structure maintains integrity during rollovers and high-impact collisions. Safety measures extend beyond the roll cage, with the entire construction of the car geared towards absorbing impacts, deflecting debris, and minimizing risks to the driver in extreme racing conditions.
Manufacturing Process
The construction of NASCAR race car bodies is a detailed process that involves skilled fabrication and precise assembly. Strict guidelines by NASCAR ensure uniformity and safety standards.
Fabrication and Assembly
Manufacturers begin with designing the body, ensuring adherence to specific dimensions and shapes according to NASCAR’s guidelines. These designs are used to create models which are then used to fabricate the actual body panels. Fabricators skillfully shape composite materials, such as a blend of fiberglass and carbon fiber, optimizing for both durability and weight. Once the panels are crafted, they move to the assembly phase, where a team of fabricators meticulously assembles the car body, often using both manual and automated techniques to ensure precision.
- Design: Adherence to NASCAR templates
- Materials: Composite (fiberglass, carbon fiber)
- Tools: Fabrication machinery, hand tools
- Skills: High precision, attention to detail
- Outcome: Panel creation, preparation for assembly
Welding and Use of Jigs
The body panels are then welded together, employing a combination of automated machinery and hand welding by experts. The use of jigs is essential during this process to hold panels in the exact position needed for proper alignment and fitting. This ensures that each body is constructed to meet rigorous specifications and maintains the integrity required for high-speed performance. Jigs facilitate the process, providing a framework that supports the components during the welding phase.
- Techniques: Automated and manual welding
- Precision: Alignment with jigs
- Outcome: Structurally sound, uniform body construction
Throughout the process, teams of fabricators and manufacturers work in unison, each bringing their specific skill set to produce the high-quality body necessary for NASCAR race cars.
Regulations and Standards
The body of a NASCAR race car is subject to stringent regulations to ensure safety, performance, and competition parity across all vehicles in the Cup Series.
Templates and Inspection
NASCAR employs a set of 30 templates that correspond to specific contours of the race car. These templates are critical during the inspection process, ensuring that each car’s body adheres to the dimensions established by NASCAR. If a car does not conform to the templates, it fails to qualify for races. Inspectors use these templates to check the shape of everything from the curve of the fender to the height of the roof, maintaining a level playing field for all competitors.
Next Gen Specifications
The NASCAR Next Gen car—introduced in the Cup Series—is the latest evolution of the stock car. It incorporates advanced specifications for both the chassis and body. Components, such as the hood and rear deck lid, are commonly made of composite materials, specifically carbon fiber. These advancements in design and material have been implemented to enhance performace, safety, and relevancy to modern production vehicles. Next Gen specifications are closely regulated to preserve the competitive balance and maintain the integrity of the sport.
Evolution and Impact
The body composition of NASCAR race cars has witnessed significant changes, advancing from mostly metal constructions to incorporating considerable amounts of carbon fiber.
Historical Changes in Design
In the early days, NASCAR vehicles were closely related to their production counterparts, with bodies made entirely of steel and minimal aerodynamic enhancements. The design of these cars closely followed the form and function of those available to the general public. However, as competition intensified and technology advanced, NASCAR race cars underwent a series of alterations aimed at improving speed and safety. The use of carbon fiber and other lightweight materials became more prevalent. Historically, the shift from stock car origins to purpose-built race machines exemplifies NASCAR’s commitment to optimizing performance and driver safety.
The shift to the Next Gen Car
With the introduction of the Gen-6 race car, NASCAR made significant strides in safety and performance, with bodies built for reduced weight and improved aerodynamics. However, the introduction of the NASCAR Next Gen car marks the latest evolutionary step in the sport’s history. The Next Gen prototype was tested in late 2021, with the car’s official debut occurring during the Busch Light Clash at the Coliseum. This new generation vehicle incorporates advanced material compositions, with a remarkable increase in carbon fiber use. The hood, part of the nose, trunk, and seat, specifically, are constructed with this lightweight material. Notably, the seat, being the largest carbon fiber part, reflects current safety priorities and weight distribution considerations. The Next Gen car represents NASCAR’s adaptation to modern racing dynamics and the continuous pursuit of technological advancement in race car development.